こんにちは。
先日は3連休でしたが、皆様は如何お過ごしになられましたでしょうか?
私も2連休を頂き子供を公園に連れて行ったりと家族サービスを致しましたが、正月休み後だったからか、心なしか人出が少なかった様に思います。
皆さん、正月にお出かけをし尽くして先週は控えたのかな?と勝手に考えていました。
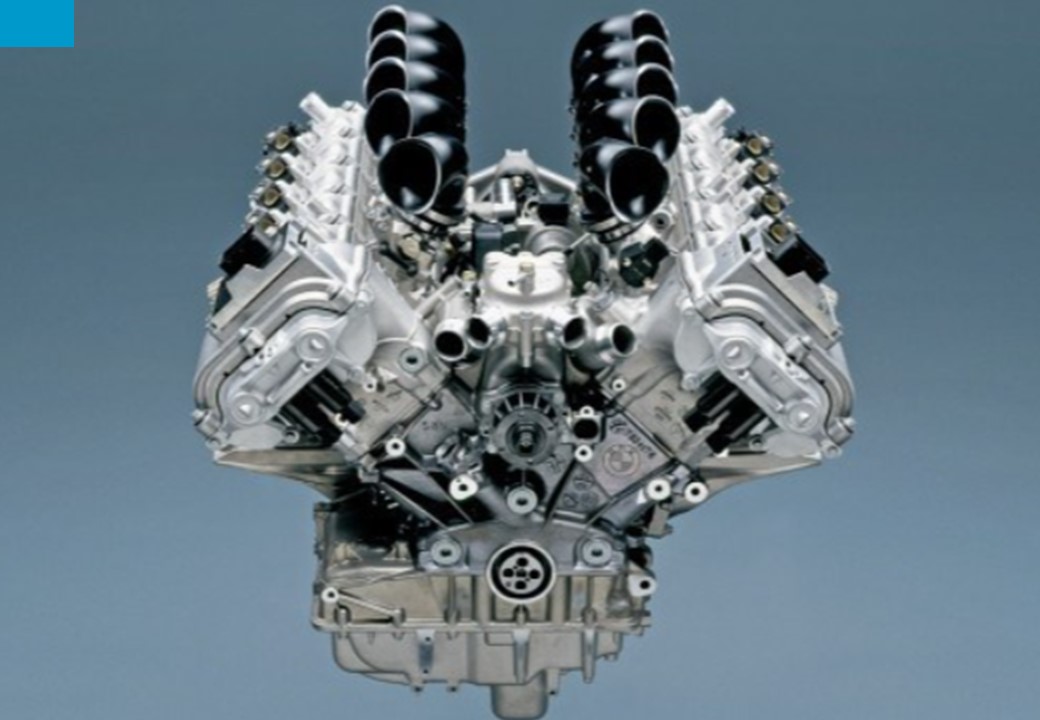
さて、間が空いてしまいましたが、今回はブログで記載をしてきた「エンジンはどのように開発されるのか」の最終となる【その3】を記載致します。
余談では御座いますが、タイトル画像のエンジンはBMWのM5に搭載されていたV10エンジンです。
これは、エンジン技術者の中では憧れのエンジンだと思います。
実際、彼我比較として、他社製エンジンをバラして検証する機会もありましたが、やはりBMW製エンジンには見どころが多かったです。
「コストをかければできるんだけどな」が言い訳でした。。。
話をエンジン開発のお話に戻しまして、【その①】【その②】で、エンジン開発フローに関してと、そのフローの中身について少し掘り下げて説明しましたが、その中で、試作エンジン、パーツで「設計」⇒「作成」⇒「テスト」⇒「テスト結果の設計への反映」⇒「作成」⇒「テスト」を何度も何度も繰り返して、目標とする性能、耐久性を発揮するエンジン諸元を確定していくと記載を致しました。
要するに、1つのエンジンに対して様々な「テスト」を繰り返し行ってエンジン仕様を決めていくことになるので、この「テスト」というのはエンジン開発において最も大事な工程とも言えます。
そして、その「テスト」の中身は大きく分けて以下の3つにカテゴライズすることが出来ます。
・性能テスト
・機能テスト
・耐久テスト
この3つのテストを多人数で計画を立てながら効率が良い方法で進めていきます。
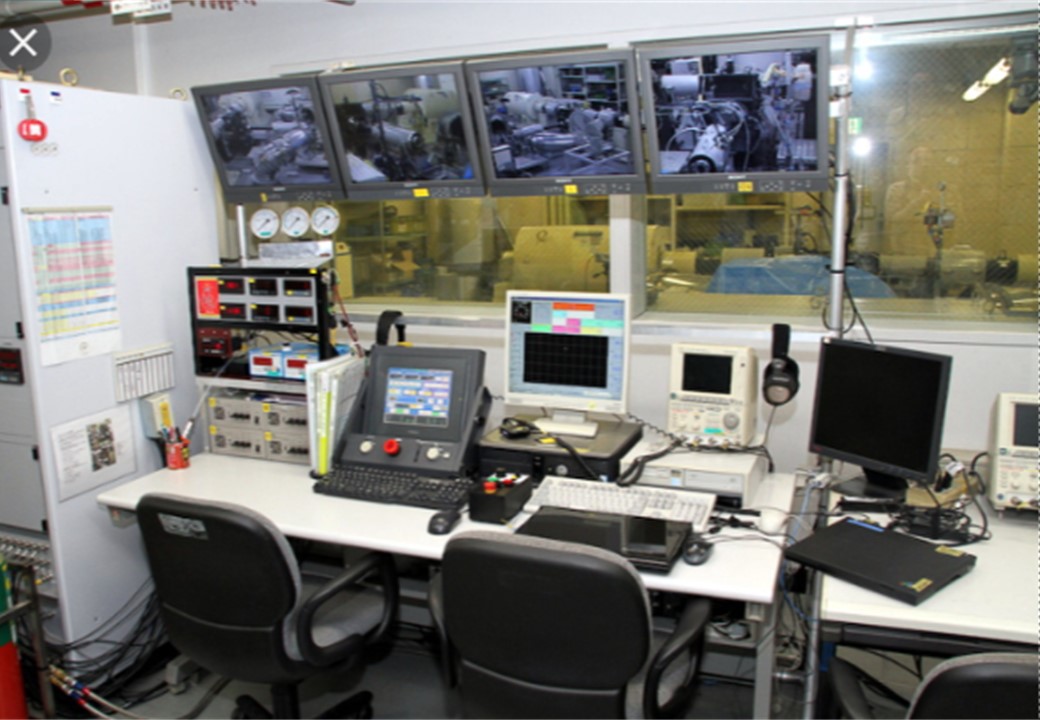
※このようなエンジンベンチと呼ばれる設備の中にエンジンをセットしてテストを行います。
ここで、各テストについて簡単に説明します。
まず、「性能テスト」・・・
これは、エンジンから発生する最高出力や最大トルクといった目標性能を達成する為の各種諸元検討をするテストで、エンジンテストと聞いて多くの方が想い浮かべるものではないでしょうか。
エンジンベンチと呼ばれる設備で、エンジン単体に吸排気系と補器類を付けた状態で実際にエンジンに火を入れてダイナモモーターを回して性能測定をし、目標性能を達成する為の圧縮比やバルブタイミング、点火時期、または吸気、排気系といったエンジンの性能に関係する各部諸元を検討していくテストです。
例えば、マフラーの直径や吸気系の長さを変化させて各回転数で性能測定を行い、良く見るエンジン性能曲線を作っていく作業です。
そして、目標とする性能曲線になるまでテストを繰り返していきます。
低速トルクが足りないから、吸気管長を伸ばすか・・・とかです。
続いて、「機能テスト」・・・
これは、オイルによる潤滑性能や冷却水による冷却性能、点火時期、バルブスプリングのバウンス限界といった、エンジンを成り立たせる為の機能性能を目標とする性能までもっていく為のテストです。
例えば、オイル関連であれば、オイルポンプの性能検討(吐出量)であったり、エンジン内部のオイル経路太さや長さ等を検討して、目標とする潤滑性能を確保する為の諸元検討をします。
冷却性能であれば、ラジエターやウォーターポンプの性能検討を行い、長時間の高負荷運転でも目標とする冷却水温度に保てるか、目標とする時間までに冷却水温度を上げることが出来るか等のテストを行います。
ノッキングテストも重要な機能テストの一つで、点火時期をどこまで進めると異常燃焼であるノッキングが発生するのかというポイントを探るテストで、点火時期を策定する際のデータとして使います。
このノッキングテストは機能テストの中で一番最初に行うテストで、このテスト結果が無いと点火時期を定めることが出来ずエンジンを回すことができない為、最優先で行います。
具体的には、エンジンに専用のノッキングセンサーを組み込み、エンジンにとって最も過酷な状況(高温)で点火時期を変えながらノッキングが発生するポイントを探っていき、ノッキングが発生しないギリギリの点火時期を設定していきます。
最後、「耐久テスト」・・・
これは、字のごとく、目標とする耐久性を確保する為に行うテストです。
これは、お客様が10年、10万キロあらゆる条件で使用しても壊れないには、どのような負荷でどれだけの時間耐久テストで持てばよいという根拠があり、その根拠に則った様々な耐久テストを行い、壊れないエンジンを作っていきます。
ちなみに、試作の砂型エンジンによるテストでは、この耐久テストで良くエンジンを壊します(笑)
そして、エンジンが壊れては、エンジンを分解してその壊れた原因を探り、壊れない様にする為にどの部品をどのように変えるのか、といったテストを重ねて、目標とする耐久性を確保できるまで、何度も耐久テストを行います。
耐久テストが無事に終わっても、エンジンを全部分解して、1点1点各部品の状態を確認しながら問題が発生する兆候が無いか確認していくという、大変時間のかかるテストです。
以上の「性能テスト」、「機能テスト」、「耐久テスト」を砂型エンジン、金型エンジンにて実施し、全ての項目において目標値を達成した時点で開発テストは終了となります。
補足となりますが、今回記載しましたのは各テストのほんの一部であり、実際は各テストの数は膨大且つそれぞれが綿密に関係している為、テストのやり直しなどは日常茶飯事で、非常に時間をかけてエンジンの開発を進めていきます。
また、これまでエンジン本体の開発に特化してお話をしましたが、実際には、排気系に関して言えば性能観点以外に、騒音規制に対応させる部門がテストをした結果をエンジンテストに反映させないといけなかったり、魅力的なサウンドの為には性能が下がる諸元が必要となり再度テストを繰り返したり。
吸気系等に関しても同様です。
よって、膨大な数のテストや設計を繰り返すだけでなく、様々な部門と絡み合っている為、各部門との調整も必要となってくる非常に大変な開発の一つと言えます。
ということで、3回に分けてエンジン開発に関して掻い摘んでご紹介してきましたが、いったんはこれにて終了としたいと思います。
3回分を通して読んで頂くと、本当に概要レベルでありますが、エンジン開発についてご理解頂けたかと思います。
話は少し変わりますが、私はかなりの数のテストをこなしましたし、多くのエンジンのトラブルを解決したり、壊してきました。
さらに、エンジン開発のプロジェクトリーダーとして全てのテストを統括して見ていたこともあり、エンジンに関してはおおよそのことはわかります。
それ故に、エンジンの吹け上がり方や、音を聞くとエンジンの調子や、どの部分が劣化しているか等の判断ができる為、中古車販売においてその知識を活かすことができると考えています。
また、当然やってはいけないこと、エンジンにとって良くないことなども、色々知っています。
その知識も、車をより良い状態に維持する為のアドバイス等に活かして行きたいと考えております。
以上、長文となりましたが、エンジンが大好きだという方で、「エンジンってどうやって開発されているのだろう?」というご興味を持てれている方の興味を満たすことになれば幸いです。
では、失礼致します。